
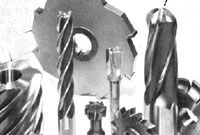
فرسایش در ابزارهای برشی(Wear in Cutting Tools)
از جمله مهمترین مسائلی كه در زمینه ماشین كاری با آن روبرو هستیم، مسأله عمر ابزار و عوامل تأثیر گذار بر روی آن است. لذا در این مقاله سعی بر این است كه بتوانیم تعریف درست و مشخصی از عمر ابزار و عوامل تأثیر گذار بر روی آن داشته باشیم و علاوه بر آن در مورد مهمترین عواملی كه تأثیر بسزایی در عمر ابزار دارند، بحث می شود.
عمر ابزار به عوامل گوناگونی وابسته است .
1. درجه حرارت(محیط و ابزار)
2. هندسه ابزار برنده
3. مایع خنك كننده
4. جنس قطعه كار از لحاظ تركیب شیمیایی
5. جنس خود ابزار
6. پارامترهای ماشین كاری (سرعت برشی، عمق براده برداری، سرعت پیشروی و...)
7. ارتعاش دستگاه
8. معیار شكست ابزار
كه از این میان معیار شكست ابزار مهمترین عامل تأثیر گذار بر عمر ابزار به شمار می آید.
معیار شكست ابزار Tool Life Criterion یك مقدار از قبل تعیین شده(بر اساس كیفیت و دقت برده برداری و ...) برای فرسایش و خوردگی ابزار یا رخ دادن یك پدیده(مانند ترك و شكست) را گویند.
عمرابزار نیز از روی همین معیار شكست تعریف می شود: زمان مورد نیاز برای رسیدن به معیار شكست.
2. معیار شكست غیر مستقیم: كه با عوامل فرسوده شدن ابزار سر و كار دارد.
ب- Fine Cracks: ترك خوردن ابزار برنده را گویند.
ج- Crater Wear , Wear Land : كه دو نوع فرسایش مستقیم و بسیار حائز اهمیت در ابزار به شمار می آیند.
این مسأله بخصوص در دستگاه های اتوماتیك (CNC) كاربرد فراوانی دارد زیار با اندازه گیری این نیروها و زمان رسیدن به حد مشخصی (كه قبلاً توضیح داده شد) می توان معیار شكست و عمر ابزار را به راحتی تخمین زد.
از عوامل گفته شده در بالا، مهمترین آنها كه تأثیر بسزایی در عمر ابزار دارد و به طور مستقیم با خود ابزار سر و كار دارد، دو نوع فرسایش اساسی در ابزار به نام Crater Wear Land است كه در ادامه این مقاله سعی بر شناسایی و راه حلهای جلوگیری از این دو فرسایش شده است.
Wear land خود به دو نوع تقسیم می شود:
1. wear land یكنواخت
2. wear land غیر یكنواخت
هر یك از این دو نوع wear land در شكل(1) نشان داده شده اند.
یك wear land كه در عمق به صورت یك نواخت و بدون شیارهای عمیق است نشان می دهد كه براده هایی كه باعث به وجود آمدن آن شده اند نازك هستند.
wear land یك نواخت حالت خوب و ایده آلی برای ابزار برشی محسوب می شود و معمولاً ابزارهایی كه مواد با سختی كم را ماشین كاری می كنند این نوع فرسایش در آنها بوجود می آید.
بیشتر اوقات یك wear land یك نواخت زمانی نمایان می شود كه ابزار، دارای برشی پیوسته با عمق براده برداری كم می باشد.
wear land غیر یك نواخت نشانه ای از براده برداری غیر پیوسته می باشد و معمولاً در ابزارهایی كه مواد با سختی بالا را براده برداری می كنند به وجود می آید. این نوع فرسایش حاصل براده برداری با عمق زیاد و سرعت برشی زیاد می باشد. حال به این بحث می پردازیم كه عمق مجاز برای یك wear land كه معیار شكست و در نتیجه عمر ابزار را تعیین می كند تا چه مقداری می تواند باشد و این عمق چگونه اندازه گیری می شود.
مباحث ارائه شده در این مقاله حاصل مطالعات و تحقیقات Mr. Leo J.St. Clair در یكی از كارگاه های ماشین كاری واقع در ایالات متحده آمریكا می باشد.
مطالعات انجام شده در زمینه سرعت سوختن نسوك ابزار نشان می دهد مواد مختلف كه ماشین كاری می شوند دارای نتیجه یكسانی نیستند و سرعت سوختن نوك ابزار با یك سرعت یك نواختی انجام می شود كه به صورت تصاعدی می باشد. مقدار سوختن نوك ابزار بوسیله عمق weae land در كنار و آخر سطح آزاد ابزار اندازه گیری می شود.
قطعات ماشین كاری شده در این تحقیق، قطعات چدنی می باشد. ابزار برشی H.S.S (و دیگر ابزارهای برشی نظیر carbide) با عمق پیشروی in 02/0 ، میانگین عمق برشی in و سرعت fmp 150 است.
تعداد قطعات ماشین كاری شده بر حسب هر in 01/0 عمق فرسایش در جدول(1) و شكل(2) نشان داده شده است. ابزار به طور كامل بعد از ماشینكاری 330 قطعه به طور كامل بعد شكسته می شود كه معادل عمق wear land در این زمان حدوداً in 06/0 است.
جدول(1) نشان می دهد كه افزایش سرعت فرسایش بعد از این كه عمق wear land از in 03/0تجاوز كرد، اتفاق می افتد كه سرعت فرسایش از این زمان به بعد تا 7 برابر سریع تر از سرعت فرسایش با عمق in 01/0 است.
ابزار حدوداً 75% عمر خود را قبل از مرحله ای كه عمق فرسایش به in 03/0 برسد، انجام می دهد و مابقی عمر خود را یعنی 25% باقیمانده را بعد از مرحله ای كه عمق فرسایش به in 03/0 می رسد، انجام می دهد. این عمل مرزی را به وجود می آورد. كه به طور قطع، غیر اقتصادی است یعنی مرزی به وجود می آید كه سرعت رسیدن به شكست عامل در این مرز بسیار زیاد است.
تحقیقات نشان می دهد كه یك ابزار carbide زمانی كه به 60/0 طول عمر خود(طول عمرابزار نقطه است كه مقدار wear land به in 06/0 برسد كه در این هنگام شكست كامل ابزار رخ می دهد) می رسد و یك ابزار H.S.S یا ابزار آلیاژی زمانی كه به 70% طول عمر خود می رسد باید تعویض و سنگ زنی شود و همان طور كه گفته شد این موقعیت در جدول (1) و شكل (2) به صورت شماتیك نشان داده شده است(كه این نتایج حاصل استفاده از میكروسكوپ های نوری می باشد.) در شكل (A-2) ملاحظه می شود كه نقطه طول عمر اقتصادی برای ابزار H.S.S حدوداً 75% طول عمر ممكن ابزار است و بعد از ماشینكاری 250 قطعه از كل تعداد قطعات كه 330 قطعه است ابزار باید سنگ زنی شود و 80 قطعه آخر تحت شرایطی ماشین كاری
می شوند كه ابزار سنگ خورده باشد.
هم چنین برای یك ابزار carbide نقطه تعویض ابزار وسنگ زنی آن، حدود 60% عمر كل ابزار است كه در این زمان 190 تا 200 قطعه ماشین كاری می شود. دلیل این كه چرا یك ابزار carbide باید زودتر از یك ابزار H.S.S و یا ابزار آلیاژی سنگ زنی شود آن است كه ابزار carbide دارای شكنندگی زیادتری می باشد كه این خاصیت شكنندگی بیشتر سبب می شود هنگامی كه wear land عمیق تر می شود نوك ابزار به راحتی شكسته شود.
زمانی كه wear land عمیق تر می شود فشار زیادی از طرف قطعه كار بر روی سطح wear land وارد می شود و وقتی ابزار carbide باشد این فشار به طور پیوسته شوكی را به وجود می آورد كه باعث می شود ابزار لب پر شود. لب پر شدن بدین معناست كه نوك ابزار شكسته می شود و همان طور كه گفته شد این دلیل عمق زیاد wear land و فشار پیوسته ناشی از قطعه كار بر روی سطح wear land می باشد مطالب گفته شده در شكل(B-2) نشان داده شده است.لب پریدگی به ندرت در ابزارهای H.S.S و آلیاژی رخ می دهد و این به دلیل سختی و چقرمگی خوب آنها می باشد.
اگر شكستگی زیاد باشد ابزار خوب و كاملاً غیر قابل استفاده می شود از این رو به دلیل آسیب زیاد ناشی از فشار wear land ، نقطه برگشتی ابزار carbide برای سنگ زنی باید 60% طول عمرش باشد كه این برخلاف مقدار 70% برای ابزارهای برشی دیگر(H.S.S) می باشد.
روش دیگری برای اندازه گیری عمق مجاز wear land وجود دارد كه بر اساس تعریف زیر از عمیق مجاز به دست می آید: ثابت نگه داشتن یك نقطه تعویض ابزار در تولید انبوه.
این تعریف بدین معناست كه با در نظر گرفتن دقت كاری و قطعه كار و كیفیت سطح مورد نیاز در تولید انبوه، آخرین قطعه ای كه دارای دقت و كیفیت لازم است را به عنوان نقطه تعویض ابزار و عمق wear land در این زمان را عمق مجاز در نظر می گیریم.
عمق مجاز wear land كه از فرسایش مخرب ابزار جلوگیری می كند، به اندازه ابزار نیز بستگی دارد. یك ابزار توانایی پراكنده سازی گرمایی بهتری نیست به یك ابزار كوك دارد. از این رو در ابزارهای بزرگ به دلیل پراكنده سازی گرمایی زیاد و زمان زیاد برای بالا رفتن دمای نوك ابزار، فرسایش به كندی انجام می شود.
عمق مجاز wear land نسبت به اندازه ابزار در زیر آمده است:
up to ½ (in) squar 1/32(in)
3/4 (in) and 1 (in) squar 3/64 (in)
(in) and (in) squar 1/16 (in)
2(in) squar or more 1/8 (in)
عمق مجاز wear land در نزدیكی نقطه پرداختكاری ابزار بیشتر از نقاط دیگر است.این قسمت وخیم ترین قسمت لبه برشی است زیرا بیشتر گرما در این قسمت متمركز است. از این رو زمانی كه wear land مشاهده می شود بهتر است اندازه آن در نزدیكی نقطه پرداختكاری ابزار اندازه گیری شود.
فرورفتگی هایی در سطح بالایی ابزار، نزدیك به لبه برشی می شود. نیروهای فرسایشی سخت كه در برابر جریان براده مقاومت می كنند عامل به وجود آمدن این نوع فرورفتگی ها هستند. این نوع فرسایش را اصطلاحاً crater می گویند.
رشد crater در ابتدای امر به كندی انجام می گیرد اما با رسیدن به مقدار معینی، سرعت رشد افزایش می یابد. این به دلیل افزایش زیاد نیروهای فرسایشی در سطح بالا می باشد.
سطح زیر وسخت بالایی ابزار مقاومت در برابر جریان براده را افزایش می دهد و در نتیجه عمل فرسایش سریع تر انجام می شود.
با ادامه این عمل (فرسایش در سطح بالا)، Crater به سمت لبه برشی پیشرفت می كند كه باعث می شود شرایط لبه بسیار ضعیف شود و این معمولاً شكست سخت لبه برش را به دنبال دارد. رشد یك Crater و تأثیر آن در شكل (A-3) نشان داده شده است.
شكل(B-3) چندین تغییر مهم را كه در منطقه نزدیك لبه برش، هنگامی كه Crater رخ می دهد، نشان می دهد.
اولین تغییری كه ایجاد می شود این است كه زاویه شیب برش(زاویه براده) از زاویه شیب مؤثر كمتر می شود(زاویه شیب مؤثر، زاویه بین نقطه تلاقی جایی كه شعاع Crater با سطح تماس می گیرد و سطح افقی را گویند) با افزایش عمق Crater این زاویه مقداری بین 30 تا 50 درجه تغییر می كند.
اندازه زیاد زاویه شیب مؤثر، لبه ابزار را به مقدار زیادی ضعیف می كند و غالباً باعث شكست لبه برش می شود.
دومین تغییری كه انجام می شود آن است كه شعاع براده كاهش می یابد و باعث می شود شعاع و اندازه Crater افزایش یابد.
در ابتدای انجام عمل برش غالباً خواهیم دید كه براده در شعاع یا قوس بزرگ بوجود می آید اما هنگامی كه ابزار فرسوده می شود شعاع براده كوچكتر می شود و براده ها غالباً تكه تكه هستند. این نشان میدهد كه Crater بزرگتر و عمیق تر شده است. بدین وسیله براده ها به صورت دایره های سخت از قطعه جدا می شوند.
شكست ابزار غالباً در این هنگام به وسیله اندازه براده پیش بینی می شود. وقتی كه ابزار در نتیجه Crater در حال شكست است، طول براده كوچك می باشد (غالباً یبن in تا in ) و باید در این هنگام از شكست كامل ابزار از طریق سنگ زنی و پرداختكاری دقیق مجدد، جلوگیری كنیم.
سومین تغییری كه دیده می شود آن است كه اندازه لبه built-up تغییر می كند. وقتی Crater به سمت لبه برشی پیش می رود، این لبه (built -up) كوچكتر می شود.
اندازه لبه built-up به گسترش شیب مؤثر بستگی دارد. یعنی این كه وقتی Crater بزرگتر می شود شیب مؤثر افزایش می یابد كه در نتیجه این عمل اندازه لبه built - up كاهش می یابد.
ابزاری كه بتواند در برابر رشد Crater مقاومت زیادی داشته باشد، از طول عمر بیشتری نسبت به ابزاری كه مقاومت كمتری در براب Crater دارد، برخوردار می باشد.
هر چیزی كه شروع و رشد یك Crater مقاومت زیادی داشته باشد، از طول عمر بیشتری نسبت به ابزاری كه مقاومت كمتری در برابر Crater دارد، برخوردار می باشد.
هر چیزی كه شروع و رشد یك Crater را به تأخیر بیاندازد، در افزایش طول عمر ابزار مؤثر است.
چگونه شروع یك Crater را به تأخیر بیندازیم؟
توسعه منطقه Crater بستگی زیادی به دو فاكتور دارد:
1. واحد فشار وارد بر لبه
2. مقاومت در برابر جریان براده
با مینیمم كردن این دو عامل می توانیم شروع یك Crater را و در نتیجه رشد آن را به تأخیر بیندازیم.
واحد فشار وارد برلبه به مقدار براده برداری و زاویه برش بستگی دارد. وقتی براده برداری از قطعه كم و به صورت آهسته انجام شود، Crater نسبت به هنگامی كه براده برداری زیاد است، نزدیك تر به لبه برش شروع به شكل گیری می كند. از این رو با افزایش بار، Crater در فاصله زیادی از لبه برش شروع به شكل گیری و رشد می كند و این، زمان زیادی را می خواهد تا این كه رشد Crater برای لبه برشی مخرب باشد.(واحد فشار وارد بر لبه با نزدیك شدن Crater به لبه برش افزایش می یابد.)
مقدار زاویه برش تأثیر قطعی در واحد فشار وارد بر لبه برش و از این رو در شكل گیری Crater دارد. بزرگ شدن زاویه برش باعث كم شدن واحد فشار لبه می شود(شاید دلیلش همان شكل گیری Crater درمناطق دور از لبه برش باشد.)
بنابراین برای به تأخیر انداختن شروع یك Crater زاویه برشی را تا حد امكان باید افزایش داد.
مقاومت در برابر جریان براده شاید مهمترین عامل درتوسعه Crater باشد. هر چیزی كه بتواند این مقاومت را كاهش دهد در شكل گیری Crater تأخیر ایجاد می كند و در نتیجه عمر ابزار را افزایش می دهد. حال چگونه مقاومت در برابر جریان براده را كاهش دهیم.
سه راه حل مهم در كاهش مقاومت در برابر جریان براده وجود دارد:
1. پرداختكاری دقیق و جلا دادن سطح بالای بازار
2. سنگ زنی در جهت جریان براده
3. انتخاب یك روان ساز مناسب كه فرسایش بین جریان براده و سطح بالا را كاهش دهد.
از این سه راه حل، راه حل های اول و دوم معمولاً شكل گیری Crater را بیشتر به تأخیر می اندازند و باعث افزایش بیشتر طول عمر ابزار نسبت به راه حل سوم می شوند. حال به تجزیه و تحلیل این دو راه حل می پردازیم.
درجه پرداخت كاری در سطح بالا در تشكیل Crater و طول عمر ابزار دخالت دارد.
اگر سطح بالایی ابزار توسط یك چرخ زبر و خشن سنگ زنی شود یك سری از شیارهای نسبتاً عمیق در سطح بالایی ابزار شكل می گیرد كه به creating hills valleys معروفند(شكل 4)
زمانی كه نوك های hills باریك و نسبتاً كوچك هستند، سطح تماس براده با سطح بالایی ابزار بسیار جزیی است و در نتیجه مقاومت سطحی كمی در برابر جریان براده خواهیم داشت كه این منجر به تأخیر در شكل گیری و رشد Crater می شود.
اما زمانی كه نوك های hills در اثر جریان براده ساییده و خورده می شوند، سطح تماس براده با سطح بالایی ابزار افزایش می یابد كه این منجر به رشد سریع Crater در سطح بالا می شود.
پرداختكاری دقیق می تواند شروع Crater را به تأخیر بیاندازد. شیارها در یك پرداخت كاری دقیق خیلی كوچك و در عین حال بسیار زیاد هستند و براده برخلاف تعداد زیادی از نوك hills جریان می یابد. در این حال سطح تماس براده با سطح بالایی ابزار بسیار كم است و همین باعث به تأخیر افتادن شكل گیری و رشد Crater می شود.
جهت سنگ زنی در سطح بالا، تأثیر بسزایی در مقاومت در برابر جریان براده دارد.
برا این كه یك مقاومت مینیمم را در برابر جریان براده داشته باشیم. باید خط های سنگ زنی در سطح بالایی ابزار جهش یكسان با جهت جریان براده داشته باشد.
اگر خط های سنگ زنی زاویه ای متضاد نسبت به جهت جریان براده داشته باشند باعث افزایش مقاومت در برابر جریان براده شده و در نتیجه شكل گیری و رشد Crater به همراه خواهند داشت.
در آزمایشاتی كه به عمل آمد نشان داده شد در ابزارهایی كه جهت سنگ زنی آنها با جهت جریان براده یكسان است، عمر آنها 30% بیشتر از عمر ابزارهایی است كه جهت سنگ زنی آنها برخلاف جهت جریان براده است.
ممكن است شرایطی بوجود آید كه هم جهت سازی خط های سنگ زنی با جهت جریان براده بسیار مشكل باشد مانند ابزارهای فرم تراشی. در اینجا هم ممكن است كارهایی بتوانیم انجام دهیم كه جهت این گونه خطاها(خط های سنگ زنی) را آن قدر تغییر دهیم كه در جهت درست قرار گیرد. این عمل به وسیله سنگ زنی قسمت های نزدیك به لبه برشی انجام می شود كه این موضوع در شكل (5) نشان داده شده است.
برای كاستن زمان سنگ زنی، سنگ باید طوری قرار گیرد كه زاویه آن با زاویه لبه برش 1 تا 3 درجه اختلاف داشته باشد. این عمل سطح باریكی را كه حدوداً عرض آن in 1/0 می باشد به وجود می آورد. حركت سنگ باید در جهت جریان براده باشد. این عمل تا زمانی كه خط های سنگ زنی هم جهت با جریان براده شوند، باید ادامه پیدا كند.
در آخر پیشنهاد می شود كه سنگ زنی همه شكل از ابزارها باید به صورت گفته شده انجام شود یعنی سعی كنیم خط های سنگ زنی در جهت جریان براده باشند كه قیمت عرف ابزار و افزایش عمر ابزار را در این كار به دنبال خواهد داشت كه بسیار باارزش و معتبر است. به علاوه پرداخت كاری بهتر قطعه كار نیز نتیجه این كار است.
منبع:www.a-faniyazd.mihanblog.com
/س
عمر ابزار به عوامل گوناگونی وابسته است .
1. درجه حرارت(محیط و ابزار)
2. هندسه ابزار برنده
3. مایع خنك كننده
4. جنس قطعه كار از لحاظ تركیب شیمیایی
5. جنس خود ابزار
6. پارامترهای ماشین كاری (سرعت برشی، عمق براده برداری، سرعت پیشروی و...)
7. ارتعاش دستگاه
8. معیار شكست ابزار
كه از این میان معیار شكست ابزار مهمترین عامل تأثیر گذار بر عمر ابزار به شمار می آید.
معیار شكست ابزار Tool Life Criterion یك مقدار از قبل تعیین شده(بر اساس كیفیت و دقت برده برداری و ...) برای فرسایش و خوردگی ابزار یا رخ دادن یك پدیده(مانند ترك و شكست) را گویند.
عمرابزار نیز از روی همین معیار شكست تعریف می شود: زمان مورد نیاز برای رسیدن به معیار شكست.
انواع معیارهای شكست
2. معیار شكست غیر مستقیم: كه با عوامل فرسوده شدن ابزار سر و كار دارد.
انواع معیار شكست مستقیم
ب- Fine Cracks: ترك خوردن ابزار برنده را گویند.
ج- Crater Wear , Wear Land : كه دو نوع فرسایش مستقیم و بسیار حائز اهمیت در ابزار به شمار می آیند.
انواع معیار شكست غیر مستقیم
الف- نیروهای براده برداری:
این مسأله بخصوص در دستگاه های اتوماتیك (CNC) كاربرد فراوانی دارد زیار با اندازه گیری این نیروها و زمان رسیدن به حد مشخصی (كه قبلاً توضیح داده شد) می توان معیار شكست و عمر ابزار را به راحتی تخمین زد.
ب- كیفیت سطح
از عوامل گفته شده در بالا، مهمترین آنها كه تأثیر بسزایی در عمر ابزار دارد و به طور مستقیم با خود ابزار سر و كار دارد، دو نوع فرسایش اساسی در ابزار به نام Crater Wear Land است كه در ادامه این مقاله سعی بر شناسایی و راه حلهای جلوگیری از این دو فرسایش شده است.
Wear Land:
Wear land خود به دو نوع تقسیم می شود:
1. wear land یكنواخت
2. wear land غیر یكنواخت
هر یك از این دو نوع wear land در شكل(1) نشان داده شده اند.
یك wear land كه در عمق به صورت یك نواخت و بدون شیارهای عمیق است نشان می دهد كه براده هایی كه باعث به وجود آمدن آن شده اند نازك هستند.
wear land یك نواخت حالت خوب و ایده آلی برای ابزار برشی محسوب می شود و معمولاً ابزارهایی كه مواد با سختی كم را ماشین كاری می كنند این نوع فرسایش در آنها بوجود می آید.
بیشتر اوقات یك wear land یك نواخت زمانی نمایان می شود كه ابزار، دارای برشی پیوسته با عمق براده برداری كم می باشد.
wear land غیر یك نواخت نشانه ای از براده برداری غیر پیوسته می باشد و معمولاً در ابزارهایی كه مواد با سختی بالا را براده برداری می كنند به وجود می آید. این نوع فرسایش حاصل براده برداری با عمق زیاد و سرعت برشی زیاد می باشد. حال به این بحث می پردازیم كه عمق مجاز برای یك wear land كه معیار شكست و در نتیجه عمر ابزار را تعیین می كند تا چه مقداری می تواند باشد و این عمق چگونه اندازه گیری می شود.
مباحث ارائه شده در این مقاله حاصل مطالعات و تحقیقات Mr. Leo J.St. Clair در یكی از كارگاه های ماشین كاری واقع در ایالات متحده آمریكا می باشد.
مطالعات انجام شده در زمینه سرعت سوختن نسوك ابزار نشان می دهد مواد مختلف كه ماشین كاری می شوند دارای نتیجه یكسانی نیستند و سرعت سوختن نوك ابزار با یك سرعت یك نواختی انجام می شود كه به صورت تصاعدی می باشد. مقدار سوختن نوك ابزار بوسیله عمق weae land در كنار و آخر سطح آزاد ابزار اندازه گیری می شود.
قطعات ماشین كاری شده در این تحقیق، قطعات چدنی می باشد. ابزار برشی H.S.S (و دیگر ابزارهای برشی نظیر carbide) با عمق پیشروی in 02/0 ، میانگین عمق برشی in و سرعت fmp 150 است.
تعداد قطعات ماشین كاری شده بر حسب هر in 01/0 عمق فرسایش در جدول(1) و شكل(2) نشان داده شده است. ابزار به طور كامل بعد از ماشینكاری 330 قطعه به طور كامل بعد شكسته می شود كه معادل عمق wear land در این زمان حدوداً in 06/0 است.
جدول(1) نشان می دهد كه افزایش سرعت فرسایش بعد از این كه عمق wear land از in 03/0تجاوز كرد، اتفاق می افتد كه سرعت فرسایش از این زمان به بعد تا 7 برابر سریع تر از سرعت فرسایش با عمق in 01/0 است.
ابزار حدوداً 75% عمر خود را قبل از مرحله ای كه عمق فرسایش به in 03/0 برسد، انجام می دهد و مابقی عمر خود را یعنی 25% باقیمانده را بعد از مرحله ای كه عمق فرسایش به in 03/0 می رسد، انجام می دهد. این عمل مرزی را به وجود می آورد. كه به طور قطع، غیر اقتصادی است یعنی مرزی به وجود می آید كه سرعت رسیدن به شكست عامل در این مرز بسیار زیاد است.
تحقیقات نشان می دهد كه یك ابزار carbide زمانی كه به 60/0 طول عمر خود(طول عمرابزار نقطه است كه مقدار wear land به in 06/0 برسد كه در این هنگام شكست كامل ابزار رخ می دهد) می رسد و یك ابزار H.S.S یا ابزار آلیاژی زمانی كه به 70% طول عمر خود می رسد باید تعویض و سنگ زنی شود و همان طور كه گفته شد این موقعیت در جدول (1) و شكل (2) به صورت شماتیك نشان داده شده است(كه این نتایج حاصل استفاده از میكروسكوپ های نوری می باشد.) در شكل (A-2) ملاحظه می شود كه نقطه طول عمر اقتصادی برای ابزار H.S.S حدوداً 75% طول عمر ممكن ابزار است و بعد از ماشینكاری 250 قطعه از كل تعداد قطعات كه 330 قطعه است ابزار باید سنگ زنی شود و 80 قطعه آخر تحت شرایطی ماشین كاری
می شوند كه ابزار سنگ خورده باشد.
هم چنین برای یك ابزار carbide نقطه تعویض ابزار وسنگ زنی آن، حدود 60% عمر كل ابزار است كه در این زمان 190 تا 200 قطعه ماشین كاری می شود. دلیل این كه چرا یك ابزار carbide باید زودتر از یك ابزار H.S.S و یا ابزار آلیاژی سنگ زنی شود آن است كه ابزار carbide دارای شكنندگی زیادتری می باشد كه این خاصیت شكنندگی بیشتر سبب می شود هنگامی كه wear land عمیق تر می شود نوك ابزار به راحتی شكسته شود.
زمانی كه wear land عمیق تر می شود فشار زیادی از طرف قطعه كار بر روی سطح wear land وارد می شود و وقتی ابزار carbide باشد این فشار به طور پیوسته شوكی را به وجود می آورد كه باعث می شود ابزار لب پر شود. لب پر شدن بدین معناست كه نوك ابزار شكسته می شود و همان طور كه گفته شد این دلیل عمق زیاد wear land و فشار پیوسته ناشی از قطعه كار بر روی سطح wear land می باشد مطالب گفته شده در شكل(B-2) نشان داده شده است.لب پریدگی به ندرت در ابزارهای H.S.S و آلیاژی رخ می دهد و این به دلیل سختی و چقرمگی خوب آنها می باشد.
اگر شكستگی زیاد باشد ابزار خوب و كاملاً غیر قابل استفاده می شود از این رو به دلیل آسیب زیاد ناشی از فشار wear land ، نقطه برگشتی ابزار carbide برای سنگ زنی باید 60% طول عمرش باشد كه این برخلاف مقدار 70% برای ابزارهای برشی دیگر(H.S.S) می باشد.
روش دیگری برای اندازه گیری عمق مجاز wear land وجود دارد كه بر اساس تعریف زیر از عمیق مجاز به دست می آید: ثابت نگه داشتن یك نقطه تعویض ابزار در تولید انبوه.
این تعریف بدین معناست كه با در نظر گرفتن دقت كاری و قطعه كار و كیفیت سطح مورد نیاز در تولید انبوه، آخرین قطعه ای كه دارای دقت و كیفیت لازم است را به عنوان نقطه تعویض ابزار و عمق wear land در این زمان را عمق مجاز در نظر می گیریم.
عمق مجاز wear land كه از فرسایش مخرب ابزار جلوگیری می كند، به اندازه ابزار نیز بستگی دارد. یك ابزار توانایی پراكنده سازی گرمایی بهتری نیست به یك ابزار كوك دارد. از این رو در ابزارهای بزرگ به دلیل پراكنده سازی گرمایی زیاد و زمان زیاد برای بالا رفتن دمای نوك ابزار، فرسایش به كندی انجام می شود.
عمق مجاز wear land نسبت به اندازه ابزار در زیر آمده است:
up to ½ (in) squar 1/32(in)
3/4 (in) and 1 (in) squar 3/64 (in)
(in) and (in) squar 1/16 (in)
2(in) squar or more 1/8 (in)
عمق مجاز wear land در نزدیكی نقطه پرداختكاری ابزار بیشتر از نقاط دیگر است.این قسمت وخیم ترین قسمت لبه برشی است زیرا بیشتر گرما در این قسمت متمركز است. از این رو زمانی كه wear land مشاهده می شود بهتر است اندازه آن در نزدیكی نقطه پرداختكاری ابزار اندازه گیری شود.
Crater
فرورفتگی هایی در سطح بالایی ابزار، نزدیك به لبه برشی می شود. نیروهای فرسایشی سخت كه در برابر جریان براده مقاومت می كنند عامل به وجود آمدن این نوع فرورفتگی ها هستند. این نوع فرسایش را اصطلاحاً crater می گویند.
رشد crater در ابتدای امر به كندی انجام می گیرد اما با رسیدن به مقدار معینی، سرعت رشد افزایش می یابد. این به دلیل افزایش زیاد نیروهای فرسایشی در سطح بالا می باشد.
سطح زیر وسخت بالایی ابزار مقاومت در برابر جریان براده را افزایش می دهد و در نتیجه عمل فرسایش سریع تر انجام می شود.
با ادامه این عمل (فرسایش در سطح بالا)، Crater به سمت لبه برشی پیشرفت می كند كه باعث می شود شرایط لبه بسیار ضعیف شود و این معمولاً شكست سخت لبه برش را به دنبال دارد. رشد یك Crater و تأثیر آن در شكل (A-3) نشان داده شده است.
شكل(B-3) چندین تغییر مهم را كه در منطقه نزدیك لبه برش، هنگامی كه Crater رخ می دهد، نشان می دهد.
اولین تغییری كه ایجاد می شود این است كه زاویه شیب برش(زاویه براده) از زاویه شیب مؤثر كمتر می شود(زاویه شیب مؤثر، زاویه بین نقطه تلاقی جایی كه شعاع Crater با سطح تماس می گیرد و سطح افقی را گویند) با افزایش عمق Crater این زاویه مقداری بین 30 تا 50 درجه تغییر می كند.
اندازه زیاد زاویه شیب مؤثر، لبه ابزار را به مقدار زیادی ضعیف می كند و غالباً باعث شكست لبه برش می شود.
دومین تغییری كه انجام می شود آن است كه شعاع براده كاهش می یابد و باعث می شود شعاع و اندازه Crater افزایش یابد.
در ابتدای انجام عمل برش غالباً خواهیم دید كه براده در شعاع یا قوس بزرگ بوجود می آید اما هنگامی كه ابزار فرسوده می شود شعاع براده كوچكتر می شود و براده ها غالباً تكه تكه هستند. این نشان میدهد كه Crater بزرگتر و عمیق تر شده است. بدین وسیله براده ها به صورت دایره های سخت از قطعه جدا می شوند.
شكست ابزار غالباً در این هنگام به وسیله اندازه براده پیش بینی می شود. وقتی كه ابزار در نتیجه Crater در حال شكست است، طول براده كوچك می باشد (غالباً یبن in تا in ) و باید در این هنگام از شكست كامل ابزار از طریق سنگ زنی و پرداختكاری دقیق مجدد، جلوگیری كنیم.
سومین تغییری كه دیده می شود آن است كه اندازه لبه built-up تغییر می كند. وقتی Crater به سمت لبه برشی پیش می رود، این لبه (built -up) كوچكتر می شود.
اندازه لبه built-up به گسترش شیب مؤثر بستگی دارد. یعنی این كه وقتی Crater بزرگتر می شود شیب مؤثر افزایش می یابد كه در نتیجه این عمل اندازه لبه built - up كاهش می یابد.
ابزاری كه بتواند در برابر رشد Crater مقاومت زیادی داشته باشد، از طول عمر بیشتری نسبت به ابزاری كه مقاومت كمتری در براب Crater دارد، برخوردار می باشد.
هر چیزی كه شروع و رشد یك Crater مقاومت زیادی داشته باشد، از طول عمر بیشتری نسبت به ابزاری كه مقاومت كمتری در برابر Crater دارد، برخوردار می باشد.
هر چیزی كه شروع و رشد یك Crater را به تأخیر بیاندازد، در افزایش طول عمر ابزار مؤثر است.
چگونه شروع یك Crater را به تأخیر بیندازیم؟
توسعه منطقه Crater بستگی زیادی به دو فاكتور دارد:
1. واحد فشار وارد بر لبه
2. مقاومت در برابر جریان براده
با مینیمم كردن این دو عامل می توانیم شروع یك Crater را و در نتیجه رشد آن را به تأخیر بیندازیم.
واحد فشار وارد برلبه به مقدار براده برداری و زاویه برش بستگی دارد. وقتی براده برداری از قطعه كم و به صورت آهسته انجام شود، Crater نسبت به هنگامی كه براده برداری زیاد است، نزدیك تر به لبه برش شروع به شكل گیری می كند. از این رو با افزایش بار، Crater در فاصله زیادی از لبه برش شروع به شكل گیری و رشد می كند و این، زمان زیادی را می خواهد تا این كه رشد Crater برای لبه برشی مخرب باشد.(واحد فشار وارد بر لبه با نزدیك شدن Crater به لبه برش افزایش می یابد.)
مقدار زاویه برش تأثیر قطعی در واحد فشار وارد بر لبه برش و از این رو در شكل گیری Crater دارد. بزرگ شدن زاویه برش باعث كم شدن واحد فشار لبه می شود(شاید دلیلش همان شكل گیری Crater درمناطق دور از لبه برش باشد.)
بنابراین برای به تأخیر انداختن شروع یك Crater زاویه برشی را تا حد امكان باید افزایش داد.
مقاومت در برابر جریان براده شاید مهمترین عامل درتوسعه Crater باشد. هر چیزی كه بتواند این مقاومت را كاهش دهد در شكل گیری Crater تأخیر ایجاد می كند و در نتیجه عمر ابزار را افزایش می دهد. حال چگونه مقاومت در برابر جریان براده را كاهش دهیم.
سه راه حل مهم در كاهش مقاومت در برابر جریان براده وجود دارد:
1. پرداختكاری دقیق و جلا دادن سطح بالای بازار
2. سنگ زنی در جهت جریان براده
3. انتخاب یك روان ساز مناسب كه فرسایش بین جریان براده و سطح بالا را كاهش دهد.
از این سه راه حل، راه حل های اول و دوم معمولاً شكل گیری Crater را بیشتر به تأخیر می اندازند و باعث افزایش بیشتر طول عمر ابزار نسبت به راه حل سوم می شوند. حال به تجزیه و تحلیل این دو راه حل می پردازیم.
درجه پرداخت كاری در سطح بالا در تشكیل Crater و طول عمر ابزار دخالت دارد.
اگر سطح بالایی ابزار توسط یك چرخ زبر و خشن سنگ زنی شود یك سری از شیارهای نسبتاً عمیق در سطح بالایی ابزار شكل می گیرد كه به creating hills valleys معروفند(شكل 4)
زمانی كه نوك های hills باریك و نسبتاً كوچك هستند، سطح تماس براده با سطح بالایی ابزار بسیار جزیی است و در نتیجه مقاومت سطحی كمی در برابر جریان براده خواهیم داشت كه این منجر به تأخیر در شكل گیری و رشد Crater می شود.
اما زمانی كه نوك های hills در اثر جریان براده ساییده و خورده می شوند، سطح تماس براده با سطح بالایی ابزار افزایش می یابد كه این منجر به رشد سریع Crater در سطح بالا می شود.
پرداختكاری دقیق می تواند شروع Crater را به تأخیر بیاندازد. شیارها در یك پرداخت كاری دقیق خیلی كوچك و در عین حال بسیار زیاد هستند و براده برخلاف تعداد زیادی از نوك hills جریان می یابد. در این حال سطح تماس براده با سطح بالایی ابزار بسیار كم است و همین باعث به تأخیر افتادن شكل گیری و رشد Crater می شود.
جهت سنگ زنی در سطح بالا، تأثیر بسزایی در مقاومت در برابر جریان براده دارد.
برا این كه یك مقاومت مینیمم را در برابر جریان براده داشته باشیم. باید خط های سنگ زنی در سطح بالایی ابزار جهش یكسان با جهت جریان براده داشته باشد.
اگر خط های سنگ زنی زاویه ای متضاد نسبت به جهت جریان براده داشته باشند باعث افزایش مقاومت در برابر جریان براده شده و در نتیجه شكل گیری و رشد Crater به همراه خواهند داشت.
در آزمایشاتی كه به عمل آمد نشان داده شد در ابزارهایی كه جهت سنگ زنی آنها با جهت جریان براده یكسان است، عمر آنها 30% بیشتر از عمر ابزارهایی است كه جهت سنگ زنی آنها برخلاف جهت جریان براده است.
ممكن است شرایطی بوجود آید كه هم جهت سازی خط های سنگ زنی با جهت جریان براده بسیار مشكل باشد مانند ابزارهای فرم تراشی. در اینجا هم ممكن است كارهایی بتوانیم انجام دهیم كه جهت این گونه خطاها(خط های سنگ زنی) را آن قدر تغییر دهیم كه در جهت درست قرار گیرد. این عمل به وسیله سنگ زنی قسمت های نزدیك به لبه برشی انجام می شود كه این موضوع در شكل (5) نشان داده شده است.
برای كاستن زمان سنگ زنی، سنگ باید طوری قرار گیرد كه زاویه آن با زاویه لبه برش 1 تا 3 درجه اختلاف داشته باشد. این عمل سطح باریكی را كه حدوداً عرض آن in 1/0 می باشد به وجود می آورد. حركت سنگ باید در جهت جریان براده باشد. این عمل تا زمانی كه خط های سنگ زنی هم جهت با جریان براده شوند، باید ادامه پیدا كند.
در آخر پیشنهاد می شود كه سنگ زنی همه شكل از ابزارها باید به صورت گفته شده انجام شود یعنی سعی كنیم خط های سنگ زنی در جهت جریان براده باشند كه قیمت عرف ابزار و افزایش عمر ابزار را در این كار به دنبال خواهد داشت كه بسیار باارزش و معتبر است. به علاوه پرداخت كاری بهتر قطعه كار نیز نتیجه این كار است.
منبع:www.a-faniyazd.mihanblog.com
/س