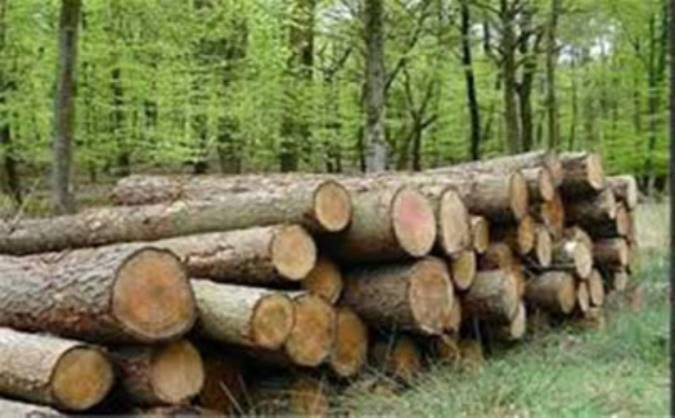
.jpg)
مترجم: حبیب الله علیخانی
عملیات های صنعتی کنونی و استفاده از دیرگدازها
صنایع شیمیایی ادوات فرآوری دارد که در گستره ی 370 تا 1870 درجه ی سانتیگراد کار می کنند. واحدهای حاوی آسترهای دیرگداز در یک بخش پالایشگاهی نمونه وار، می توانند شامل واحد کراکینگ کاتالیستی (FCCUs)، بهینه سازهای کاتالیستی، هیترهای مشعلی، بویلرها، بهینه سازهای هیدروژن، کوره های اتیلنی، مخازن مخصوص سوزاندن و کوره های کربن می باشد. برخی از این واحدها به گونه ای طراحی شده اند که قابلیت عایق کاری را دارا می باشند در حالی که برخی بخش های دیگر، واحدهای دما پایین هستند (مانند FCCUs) و از ای نرو، تنها حاوی یک لایه ی منفرد از مواد دیرگداز هستند که برای فایق آمدن بر سایش شدید ایجاد شده به دلیل کاتالیست ها، اعمال شده اند. در صنعت پتروشیمی و سنتز صنعتی گازها، طراحی های جدید در محیط حمایت کننده ی کاتالیست و عایق کاری با استفاده از دیرگدازها، موجب افزایش در عمر مفید عملیات و افزایش بازده رآکتورهای مختلف می شود. هزینه ی تخمین زده شده برای عایق کاری با آسترهای دیرگداز و کارهای نصب و نگهداری آنها در صنعت شیمیایی و پتروشیمی، نسبتاً پایین است (در واقعا مقداری نزدیک به 1 % از کل هزینه های عملیاتی). به دلیل دماهای عملیاتی پایین، در مقایسه با سایر صنایع، دیرگدازها به صورت نرمال بوسیله ی دماهای بالا تحت تأثیر قرار نمی گیرند و از این رو، تخریب ناشی از ایروژن، خوردگی و تنش های مکانیکی در آنها کمتر است. یکی دیگر از مشکلاتی که بر روی قابلیت اعتماد دیرگدازها اثر گذار است، روشی است که دیرگداز با استفاده از آن نصب می شود. علاوه بر این، آسترکاری این بخش ها، معمولاً زمان کمتری در مقایسه با آسترکاری در سایر صنایع، نیاز دارد. طراحی آسترکاری (ضخامت، نحوی چیدمان، طراحی ساختار و اتصالات مربوطه) نیز می تواند مورد توجه باشد.همچنین تناژ کلی مربوط به مواد دیرگدازی که در یک پالایشگاه نمونه وار با اندازه ی متوسط مورد استفاده قرار می گیرد، می تواند در حد 1000 تن باشد که این میزان برای حداقل یک دهه کافی است. یک پالایشگاه نمونه وار نیازمند 2500 تن دیرگداز می باشد. برخی از واحدهای حساس تر نیازمند نگهداری هستند و باید هر ساله مورد بازبینی و تعمیر و نگهداری قرار گیرند.
به طور کلی، اکثر دیرگدازهایی که بوسیله ی کارخانه جات مواد شیمیایی مورد استفاده قرار می گیرند، از نوع مونولیتیکی هستند. این دیرگدازها شامل مواد ریختنی، مخلوط های ریخته گری شده با ویبراسیون، مخلوط های چسبی، مواد ریختنی حاوی مقادیر اندک سیمان و بدون سیمان، و انواع مختلفی از دیرگدازهای عایق کاری می باشند. به دلیل اینکه بسیاری از فرایندهای پالایش کوتاه مدت می باشند، یک اتصال سرامیکی می تواند با اتصال های هیدرولیکی (سیمانی) جایگزین شود. برخی از انواع این دیرگدازها را با استفاده از پلاستیک های با اتصال فسفاتی به هم متصل می کنند. در واقع این اتصال ها نیازهای مربوط به دما پایین را برطرف می کنند. برخی از شرکت ها دارای مخلوط های ریختنی هستند که مخصوص استفاده در این بخش ها می باشند.
به هر حال، محلی که دیرگدازی پیشرفته ممکن است بیشترین اثر را بر روی بازده صنعت شیمیایی داشته باشند، بویلرها هستند که در حقیقت برای تولید جریان بخار استفاده می شوند. بهبودهای ایجاد شده در بازده گرمایی بویلرها (به خودی خود) از طریق بهبود عایق کاری بخش های داخلی و لوله های انتقال مقدور می شود. در حقیقت با استفاده از دیرگدازهای مورد استفاده در این بویلرها، میزان اتلاف حرارت به حداقل، می رسد.
در صنعت پتروشیمی و سنتز صنعتی گازها، طراحی های جدید در محیط حمایت کننده ی کاتالیست و عایق کاری با استفاده از دیرگدازها، موجب افزایش در عمر مفید عملیات و افزایش بازده رآکتورهای مختلف می شود. طراحی های جدید از دیرگدازها که در بخش حمایت کننده های کاتالیستی استفاده می شوند، موجب افزایش نرخ جریان و افزایش عمر مفید تولید کاتالیست ها می شوند. کاتالیست ها مواد گران قیمتی هستند و از این رو، این کار موجب صرفه جویی های قابل توجهی می شود. توجه زیادی باید به استفاده از مواد آسترکاری سرامیکی حاوی فیبر و همچنین مواد میکرومتخلخل سیلیسی شود. توجه زیادی نیز باید به استفاده از قطعات پیش ساخته برای استفاده در اجزای مختلف فرایندهای تولید، معطوف شود. همچنین استفاده از تکنولوژی پیش ساخته، بیشتر مد نظر می باشد. به دلیل اینکه این بسیار مهم است که دماهای مربوط به پوسته ی رآکتورها و بخش های واکنشی باید بالاتر از یک دمای آستانه قرار گیرد تا بدی صورت از ایجاد بخار بر روی سطوح رآکتورها جلوگیری به عمل آید، طراح ها تلاش می کنند تا مدل هایی برای پیش بینی گرادیان دمایی و دماهای سطح سرد رآکتورها، توسعه دهند. فقدان اطلاعات در مورد رسانایی گرمایی برخی از مواد ریختگی مونولیتیک یکی از مشکلات در این زمینه می باشد.
موانع
دیرگدازها و مواد عایق کاری نقش مهمی در بیشتر عملیات های شیمیایی دارند. این تخمین زده شده است که 50 % از انرژی که به صورت مستقیم در این فرایندها به مصرف می رسد، با دیرگدازها مرتبط است. بر اساس تجزیه و تحلیل انجام شده بر روی کوره های صنعتی و عملیات های انجام شده در این صنایع، فهمیده شده است که بهبود در سیستم دیرگداز مورد استفاده در صنایع شیمیایی و پتروشیمی، می تواند منجر به صرفه جویی قابل توجه در مصرف انرژی شود (تا میزان 266.4 TBtu در سال). موانع موجود در این زمینه، عبارتند از:• فقدان آگاهی در مورد خواص دما بالا مانند گسستگی خزشی، استحکام کوتاه مدت، رسانایی گرمایی، انبساط حرارتی، دوام و پایداری دیرگدازهای مونولیتیکی مورد استفاده در این صنایع.
• فقدان آگاهی در مورد خواص خوردگی دیرگدازهای مورد استفاده در صنایع شیمیایی و پتروشیمی.
• فقدان آگاهی در مورد زمان اتمام و هزینه های نگهداری که به صورت روزافزون بر روی المان های هزینه ای اثرگذار می باشد. فقدان آگاهی در مورد کاهش در مصرف انرژی و آلودگی هوا.
• فقدان آگاهی در مورد محیط های دما بالا و خوردنده که موجب محدود شدن عمر دیرگدازها و افزایش هزینه های نگهداری در بسیاری از رآکتورهای شیمیایی و بخش های پتروشیمی، می شود.
بیشتر بخوانید: آثار تخریب پتروشیمی بر محیط زیست
روش های تحقیق و توسعه
• توسعه ی دیرگدازهای بهبود یافته برای مینیمم کردن آسیب های مکانیکی به محفظه های با آستر دیرگداز از طریق کاهش در میزان تنش های مکانیکی بر روی آستر.• توسعه ی کارها در زمینه ی بهینه سازی خواص فیزیکی دیرگدازها (یعنی خاصیت عایق کاری گرمایی، مقاومت به ایروژن، مقاومت در برابر خوردگی، مقاومت به شوک حرارتی، استحکام، تخلخل و نفوذپذیری) تحت شرایط عملیاتی شناخته شده برای انواع واحدهای خاص. توسعه ی محصولات واقعی و با قابلیت تولید و توسعه و بهبود خواص به منظور کنترل کیفیت و بهبود خواص فیزیکی مورد نیاز برای آسترکاری در شرایط سرویس دهی.
• توسعه ی روش های بهبود یافته برای آنالیز ادوات دما بالا از طریق روش های بررسی آنلاین دیرگدازها
• توسعه ی دیرگدازهای با عمر طولانی تر که در حقیقت تردی کمتری دارند و نسبت به شوک حرارتی مقاوم تر می باشند.
• بدست آوردن داده های ترموفیزیکی، مکانیکی و کینتیکی از دیرگدازها.
• توسعه ی کامپوزیت های زمینه ی سرامیکی- فلزی با پایداری بهبود یافته و سطح اصلاح شده و یا دارای پوشش برای افزایش مقاومت به خوردگی
• توسعه ی موادی که در برابر دماهای بالا مقاوم هستند در حالی که استحکام، دوام، مقاومت به خوردگی، مقاومت به سایش و تخریب در آنها فوق العاده است.
• توسعه ی موادی که مقامت بهبود یافته ای در برابر اسیدهای آلی دارند و می توان آنها را در فرایندهای پایه کلر نیز استفاده کرد. با این کار می توان الزامات عملیاتی و حفظ و نگهداری را کاهش داد.
• توسعه ی دیرگدازها و پوشش های نسوزی که موجب کاهش مصرف انرژی و هزینه های نگهداری می شوند. توسعه ی سطوح نچسب دما بالا که در واقع بدون تخریب شدن، در دماهای بالا تبخیر می شوند و موجب کاهش هزینه های نگهداری مربوط به ادوات می شوند.
محصولات جنگلی
عملیات ها و استفاده های کنونی از مواد دیرگدازاگر چه صنعت پالپ و کاغذ یک استفاده کننده ی قابل توجه از مواد دیرگداز نیست. صنعت محصولات جنگلی سومین مصرف کننده ی بزرگ انرژی در ایالات متحده ی آمریکا می باشد. این بخش سالانه 3.3 کوارد انرژی مصرف می کند. به خاطر همین، این صنعت 63 % از انرژی خود را با استفاده از محصولات ضایعاتی چوبی بازیافت شده و سایر منابع تجدیدپذیر تولید می کند. از سال 1972، این صنعت استفاده ی خود از سوخت های فصیلی را کاهش داد و تنها 2 % از انرژی خود را خریداری کرد، در حالی که میزان تولید این بخش از زمان گفته شده تا الان، 64 % افزایش یافته است. در آینده، گازگیری از شیرآبه ی تولید کاغذ (black liquor) و بیوگاز، منجر به کاهش بیشتر انرژی خریداری شده و حتی تغییر در صنعت تولید پالپ و کاغذ می شود. بخش های گازگیری در واقع می توانند انرژی قابل توجهی تولید کنند.
کوره های بازیافت آهک نیز در تولید محصولات جنگلی استفاده می شوند. این بخش ها، به عنوان یکی از اجزای مربوط به فرایند کرافت پالپ است. این کوره ها، 7 میلیون Btu انرژی را برای بازیابی آهک مصرف می کنند. حال این کوره ها محدودیت هایی از جمله نرخ تولید سیکلی، کیفیت پایین محصول حاصله، گرد و غبار سیکلی قابل توجه، و مشکل انسداد، رنج می برند. بیشتر این محدودیت ها به دلیل خرابی در آجرکاری و یا شکست دیرگدازها رخ می دهد و می توانند موجب تعمیر و نگهداری این سیستم ها به مدت 35 روز شوند.
موانع
این تخمین زده می شود که 40 % از مصرف انرژی مستقیم بوسیله ی محصولات جنگلی، در فرایندهایی رخ می دهد که تحت تأثیر دیرگدازها می باشند. بر اساس تجزیه و تحلیل های انجام شده بر روی کوره ها و واحدهای فرآوری، این فهمیده شده است که بهبود در سیستم های دیرگداز می تواند منجر به صرفه جویی در میزان مصرف انرژی تا میزان 129 TBtu در سال شود.• فقدان آگاهی در مورد مسائل مربوط به چسبیدن مواد واکنش دهنده و محصولات به آسترهای دیرگداز و کوره ها که موجب محدود شدن عمر عملیاتی آنها می شود.
• عدم دسترسی به مواد با مقاومت خوردگی در برابر محیط های قلیایی بالا و مقاوم در برابر خوردگی و سایش، مقاومت در برابر پوسته ای شدن و تطابق گرمایی با مواد فلزی مورد استفاده در بخش های گازگیری.
• عدم دسترسی به مواد بهبود یافته که با اتمسفرهای قلیایی واکنش نمی دهند. یک چنین واکنش هایی موجب تراشیده شدن سطح آستر دیرگداز می شود و عمر آستر را کاهش می دهد.
• فقدان داده ها در مورد خواص مواد با قابلیت ریخته گری مورد استفاده در این صنعت و اطلاعات مربوط به محصولات دیرگداز موجود.
• عدم دسترسی به دیرگدازهای بهبود یافته برای بویلرهای بازیابی Tomlinson و جایگزینی با دیرگدازهای گل آتشخوار، آجرهای آلومینایی و اجزای مونولیتیکی مشابه در بخش های زیرین. دیرگدازهای بهبود یافته می توانند میزان زمان های خاموشی دستگاه را کاهش دهند.
• فقدان سیستم های دیرگداز با مقاومت به خوردگی قلیایی کافی برای آسترکاری محفظه های دخیره سازی مورد استفاده در بخش مواد شیمیایی پالپ.
روش های تحقیق و توسعه
• توسعه ی دیرگدازهای بهبود یافته برای کوره های آهک، به منظور کاهش زمان های مورد نیاز برای ایجاد رینگ و کوتینگ که منجر به افزایش بازده انرژی و طول عمر کوره• توسعه ی دیرگدازهای پیشرفته برای مهیا کردن مواد مناسب در بخش های گازگیری. دیرگدازهای پیشرفته می توانند منجر به بهبود قابل توجه در بازده انرژی برا صنعت محصولات جنگلی شوند.
• توسعه ی موادی که دارای مقاومت بیشتر در برابر خوردگی با نمک های مذاب هستند. این مواد مقاومت بیشتری در برابر ایروژن دارند و نسبت به خرد شدن نیز مقاوم ترند.
• توسعه ی مواد دیرگدازی که از لحاظ گرمایی با مواد فلزی مورد استفاده در بخش های گازگیری، تطابق داشته باشند.
استفاده از مطالب این مقاله، با ذکر منبع راسخون، بلامانع می باشد.
منبع مقاله :
Refractories for industrial processing: opportunities for improved energy efficiency/ prepared by DOE- EERE industrial technologies program